THERMAL TRANSFER VS DIRECT THERMAL PRINTING
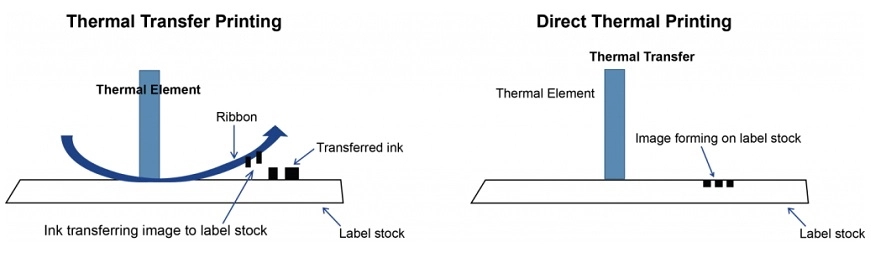
Published by - OP Team on August 5, 2019 Blog
Printers are one of the core components at a business workplace. Be it a small retail shop or a checkout counter in a shopping mall or even inside the warehouse printers are required extensively to print labels and barcodes to identify products, tag assets, etc. While printing is important part of a business process, what kind of printer should be used where is another important question to tackle. Because, using right kind of printer can drastically improve the productivity and save huge amount of time and money.
Traditionally Direct thermal printing has been around and used across several fields including retail shops, meat, dairy, etc. As the technology evolved newer systems came into market which were more efficient, reliable, and cost-effective. With the increased development in thermal paper technology wide range of products are now suitable for use in many applications across almost every market. This in-turn resulted in increased interest in Direct thermal printing as it offers cost-effective and efficient way for printing.
What are Direct Thermal and Thermal Transfer Printing?
Both the printing solutions have advantages and disadvantages of their own and choosing the one which is suitable for your business will increase the productivity. But before that let us understand the difference between both the printing methods.
Thermal Transfer
Thermal transfer printing uses a print head elements (dots) and a thin ribbon. The ribbon has a wax, resin, or wax and resin coating on one side. Heat is transferred through the print head dots which heats the backside of the ribbon melting it and, thus, transfers the compounds (wax or resin or both) on to the label material to create a printed image.
Direct Thermal
Direct thermal printing also uses a print head to print images but it does not use thin ribbons. Instead it uses heat to print on the material. This printing requires heat sensitive label material to print on. The print head comes in direct contact with the heat sensitive paper and the heat from the print head causes a change of color in the material to create printed image.
Both the technologies have some advantages and disadvantages but each one of them serves its best purpose when used in a right way. Let us have a look in detail at each aspect so that it becomes easy for you to choose which printing technology is better for your business.
Thermal Print Head
In direct thermal printing the print head is in direct contact with the label material as the print head directly prints on the material. Whereas in thermal transfer printing the thermal ribbon acts as a buffer between the print head dots and the printing material. Thermal ribbons are equipped with an additional back coating which reduces the static and friction and increases its life. But, due to the lack of ribbon, the print head in direct thermal printing suffers increased wear as compared to thermal transfer printing. As the print head is in direct contact with the printing material in direct thermal printing it constantly is exposed to friction.
Also, dust flowing around or might be on the label comes in direct contact with the print head and as this dust is pulled across the print head there is a good chance that they might burn on to the dots and physically damage them. This will result in poor print quality and decreases the life of print head too. Whereas the ribbon in thermal transfer printing prevents the dust to come in direct contact with the print head and reduces the physical damage chances.
In conclusion, print head life in direct thermal printing is considerably reduced as compared to thermal transfer printing. Therefore, direct thermal printing is mostly used in small scale businesses as they don’t need to print extensive number of labels and this technology is cost-effective for small businesses.
Printer Configuration
These days a thermal transfer printer has the configuration to print either thermal transfer or direct thermal. But if you need to print using only direct thermal technology then there are specific printers available which print only direct thermal. Such printers cost less as they don’t have additional hardware (like ribbon and ribbon controller). With lesser hardware components the printer becomes less complicated and there are only few parts to break. This printer also saves you lots of money used to purchase ribbon and saves time you would require changing the ribbon. Therefore, purchasing a direct thermal printer (if you don’t require thermal transfer printer) makes more sense. But if your organization needs to print high-quality labels that last long and take less time to print then you will require a thermal transfer.
In conclusion, a thermal transfer printer costs more as it has additional components but is necessary if you need to print high-quality labels daily. And a direct thermal printer is perfect for a small business which doesn’t require printing huge number of labels daily.
Label Life
This is a small but most important consideration as it will decide the lifetime of your product’s recognition. Direct thermal and thermal transfer offer different lifetime for a label. As a business you must know your label’s life requirement before purchasing a printer. If your product is to go through extreme conditions like extreme heat, cold, bad weather conditions then you should consider printing using a thermal transfer printer. If you own a warehouse, then your products are most likely to go through extreme conditions. If you ship pharmaceutical products or hazardous materials then information on the label is extremely crucial and, therefore, the print on label should be clear and readable. Such labels should be printed using a thermal transfer printer.
Advantages
Direct Thermal Printing | Thermal Transfer Printing |
The biggest advantage of direct thermal printing is the low printing cost. You don’t need to purchase ink, toner, or thermal ribbon. You only need to purchase labels | Best for printing higher volume labels which require long lifetime like barcodes. The ink is absorbed by the print material and lasts longer. |
Best for printing high volume printing.
|
These printers can print in color
|
Low maintenance cost
|
You can print logos and branding on your labels all in color
|
Easy to use and cost-effective.
|
The label print can withstand extreme weather conditions and can still be readable and in good condition |
Disadvantages
Direct Thermal Printing | Thermal Transfer Printing |
Not able to print in color and can only print in black
|
This printing technology are expensive as compared to direct thermal
|
Not useful for long life labels as the ink fades away after some time.
|
Thermal transfer printer uses more consumable parts like ribbon which needs to be changed from time to time
|
Labels cannot withstand extreme environmental conditions.
|
High maintenance cost
|
Conclusion
While both the printing technologies are up-to-the-mark all depends upon what kind of business you own and what are your label printing requirements. If you own a small business which does not require long-life labels, then a direct thermal printer is a best choice for you. Whereas if your business is large and your products require labels that can withstand harsh conditions then a thermal transfer is your best choice.
Choose as per your requirements and get the best printer from one of the top trusted online printer store. Avail best deals and discounts on your purchase. Buy bestselling printers online today!